What happens in the dry dock?
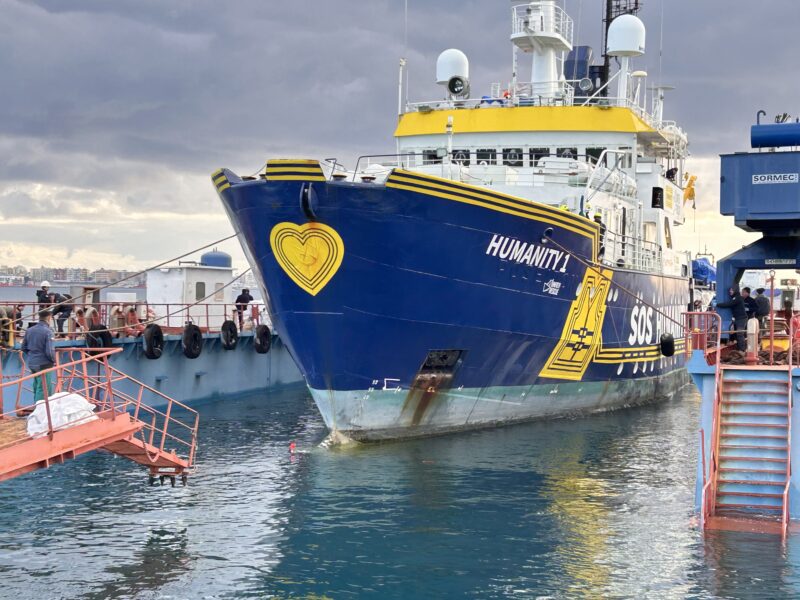
After two years of continuous service, our rescue vessel went into the shipyard at the end of 2024. Like any other ship, Humanity 1 is required to undergo periodical dry dock periods to ensure that it remains compliant and seaworthy – to hopefully return to the sea ready for many more missions!
The process of pulling an almost 200 feet long rescue ship out of the sea is certainly nothing you’ll see every day. Francis, our Fleet And Operations Coordinator, describes this moment as following:
“As the massive ship slowly emerged from the water, the sheer scale of its hull became strikingly apparent. The layers of marine growth— mussels—clinging to the underside told a story of countless miles travelled across the sea. It was a surreal sight, almost as if the ship was shedding its outer skin, exposing the hardworking foundation that had carried it through so many missions…
The sound of water dripping off the hull echoed in the dry dock, while sunlight reflected off the damp metal surface, illuminating areas in need of attention. Watching the crew and technicians gather around, pointing out sections for repair and cleaning, made me appreciate the immense effort and coordination required to maintain a vessel of this size
It was a humbling moment, a reminder of the ship’s resilience and the dedication required to keep it seaworthy. For me, it symbolised the intersection of human ingenuity and the power of the sea—a moment that will stay with me long after this phase is complete.”
In the dry dock, the ship is undergoing thorough checks and maintenance. For Humanity 1, this phase also aligns with the regulatory requirements, such as surveys to proof the ship’s classification and statutory inspections that typically occur every 5 years.

The propeller is undergoing thorough inspection and polishing, while the stern tube seals are being replaced. This ensures optimal propulsion efficiency, reduces drag, and minimises the risk of oil leakage, which is crucial for environmental compliance and maintaining the ship’s operational performance.
Layers of marine growth, including mussels and barnacles, are being removed from the hull. After cleaning, a fresh coat of anti-fouling paint is being applied. This reduces drag, improves fuel efficiency, and allows the ship to move faster and more efficiently through the water.
The vacuum tank is being replaced, involving significant structural work like cutting into the vessel’s side. This upgrade will improve the ship’s waste management system, ensuring compliance with environmental regulations and enhancing onboard hygiene.
Various systems and machinery in the engine room are being overhauled to ensure reliable operation. This includes inspecting critical components and addressing any wear and tear that could impact performance. These repairs and maintenance tasks are not only essential for the vessel’s safety but contribute to its efficiency, longevity, and readiness for future missions.
Such extensive maintenance requires a lot of hands. Currently, about 25 crew members are working to make Humanity 1 ready for its come-back at sea, including 7 volunteers.
However, maintenance is not only a task to be carried out every few weeks on land. To ensure the ship remain efficient and ready to rescue, crew members like two engineers that are always on board are constantly working on repairs and maintenance on Humanity 1.

Daily checks of critical systems, such as engines, generators, and navigation equipment, are conducted to identify and address any issues early.
The engine room team performs regular servicing of machinery, including oil changes, filter replacements, and monitoring fuel and water systems, to keep operations running smoothly.
Technicians frequently inspect and maintain electrical systems, ensuring that essential communication equipment, including AIS and radar, functions without interruption.
Life-saving equipment like life jackets, centifloat and rescue boats are regularly inspected and maintained. The deck crew also ensures that ropes, winches, and cranes are in good condition.
Saltwater exposure accelerates wear and corrosion. The deck crew conducts regular cleaning and applies anti-corrosion treatments to metal surfaces and fittings.
Minor issues, such as leaks, loose fittings, or small mechanical failures, are addressed immediately using onboard tools and spare parts.